Antimony (Sb) is a metalloid that plays a critical role in various industrial applications, particularly in flame retardants, lead-acid batteries, and as an alloying agent in metals. The primary ore from antimony is stibnite (Sb2S3). The growing demand for antimony in high-performance materials necessitates efficient extraction and purification techniques. This article provides an in-depth look at the lab antimony beneficiation process, highlighting the features of each stage of the process and detailing the equipment used in laboratory settings.
Features of Antimony Beneficiation
The antimony beneficiation process encompasses various features that enhance its efficiency and effectiveness:
Multi-Stage Process
The beneficiation process is designed as a multi-stage operation, allowing for the gradual antimony concentration while effectively removing impurities. Each stage targets specific characteristics of the ore, ensuring optimal recovery.
Adaptability
The techniques employed in the beneficiation process adapt to various types of antimony ores and their specific mineralogical properties. This adaptability is crucial, as different ores may require tailored approaches for effective processing.
Use of Gravity and Flotation Techniques
Combining gravity separation and flotation techniques capitalizes on the antimony’s physical and chemical properties, ensuring high recovery rates. Gravity methods exploit the high density of antimony, while flotation methods leverage chemical interactions to promote selective separation.
Environmental Considerations
Modern beneficiation processes prioritize minimizing ecological impacts. It includes the effective management of waste materials and the recycling of water used during processing, aligning with sustainable practices in mining and metallurgy.
Laboratory Validation
Laboratory-scale testing allows researchers and engineers to optimize the beneficiation process before scaling up to industrial operations. This validation is critical for developing efficient and cost-effective processing methods.
Lab Antimony Beneficiation Process
The laboratory beneficiation process for antimony involves several key stages, each requiring specific equipment. Below is a detailed description of each stage, its objectives, and the equipment used.
1. Crushing and Grinding
The first stage of the antimony beneficiation process involves crushing and grinding the ore to liberate the antimony minerals from the gangue. This step is crucial, as the size reduction enhances the surface area for subsequent processing.
Equipment Used:
- Lab Jaw Crusher: The jaw crusher is typically the primary equipment in the crushing process. It compresses the ore between two plates, generating significant force to fracture the material. It is essential for crushing large pieces of ore into smaller fragments suitable for further processing.
- Lab Hammer Crusher: The lab hammer crusher is suitable for secondary crushing. It further reduces the particle size by impact between hammers. This equipment is ideal for achieving a finer particle size for optimal grinding.
- Ball Mill: After the crushing stage, the ore enters a ball mill to grind the material into a fine powder. The ball mill consists of a rotating cylindrical shell filled with steel balls that grind the ore through impact and abrasion. This fine grinding is critical for liberating antimony minerals from the gangue.
2. Gravity Separation
After grinding, the minerals enter gravity separation equipment to concentrate the antimony. Considering antimony has a higher specific gravity than many gangue materials, gravity methods can effectively separate valuable minerals.
Equipment Used:
- Shaking Table: A shaking table is a gravity separation device that uses a shaking motion and water flow to separate particles based on density. The shaking table is effective for concentrating fine antimony particles, allowing for the separation of heavier minerals from lighter gangue materials. The table surface is coated with a thin layer of water that helps facilitate particle movement.
- Jigging Machine: Jigs utilize pulsating water to separate heavier minerals from lighter ones. Feed the ore into the jig separator. The denser antimony minerals settle at the bottom, and lighter gangue materials will wash away. Jigs are effective for recovering coarse particles and are adjustable for different ore types.
- Spiral Concentrator: This equipment employs a spiral-shaped channel to exploit differences in density and particle size. The slurry flows down the spiral, where the centrifugal force causes denser antimony particles to move toward the inner part of the spiral while lighter particles are carried away. Spiral concentrators are efficient for the continuous processing of large volumes of ore.
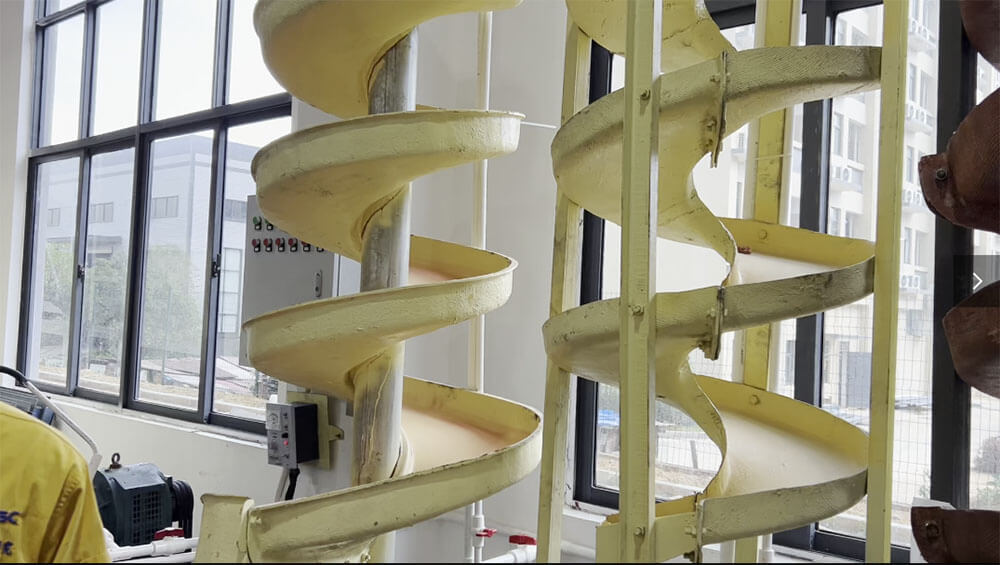
3. Flotation
Flotation is a widely used method in mineral processing for separating valuable minerals from gangue based on their surface properties. This process involves adding chemicals (reagents) to the ore slurry to promote the attachment of antimony minerals to air bubbles, allowing them to float to the surface.
Equipment Used:
- Flotation Cell: The flotation cell is the primary equipment used in this stage. It consists of a tank where the ore slurry mixes with air and flotation reagents. Stirring slurry creates bubbles that selectively attach to the antimony particles, causing them to rise to the surface and form a foam.
- Mixing Tank with Agitator: A mixing tank mixes the slurry with reagents. Proper agitation is essential for maintaining uniform particle distribution in the flotation cell. It enhances the overall efficiency of the flotation process.
- Reagents Dispenser: Precise dosing of reagents is critical for efficient flotation. The reagents dispenser allows extra specific chemicals, such as collectors and frothers, to optimize the separation process. Collectors enhance the hydrophobicity of the antimony particles, while frothers stabilize the foam at the surface.
4. Magnetic Separation
In certain circumstances, magnetic separation can purify the antimony concentrate by removing ferromagnetic impurities.
Equipment Used:
- Magnetic Separator: This equipment uses a magnetic field to attract and remove ferromagnetic materials from the antimony concentrate. Magnetic separators can be used as a secondary stage after flotation to enhance the purity of the final product. Based on the magnetic susceptibility of the impurities present adjust the separation process.
5. Roasting and Reduction
After the antimony concentration, the following steps involve roasting the concentrate to remove sulfur and other impurities, followed by reduction to produce metallic antimony.
Equipment Used:
- Rotary Kiln: The rotary kiln is for the roasting process, where the antimony concentrate is heated in the air. This process converts sulfides into oxides, releasing sulfur dioxide gas and allowing for the removal of impurities.
- Reduction Furnace: Following roasting, the antimony oxide can be reduced to metallic antimony using carbon or other reducing agents. The reduction furnace provides the necessary high temperatures to facilitate this chemical reaction.
6. Refining
The final stage of the process may involve further refining of the metallic antimony to achieve the desired purity levels.
Equipment Used:
- Electrolytic Cell: This equipment is used for the electrolysis of antimony, allowing for the purification of the metallic product. During electrolysis, an electric current is passed through a solution containing antimony ions, causing them to deposit onto an electrode, resulting in high-purity metallic antimony.
- Vacuum Distillation Unit: This equipment further refines metallic antimony, removing residual impurities through the heat in a vacuum environment. Vacuum distillation is an effective method of achieving high-purity antimony by separating it from other volatile impurities.
The laboratory beneficiation process for antimony is a comprehensive and multi-step procedure requiring various specialized equipment. Each stage, crushing, grinding, gravity separation, and flotation, is irreplaceable in efficiently extracting and purifying antimony from its ores. Understanding the intricacies of the antimony beneficiation process aids in resource management and contributes to sustainable practices.
Conclusion
With the increasing demand for antimony in various industries, optimizing these processes and the associated equipment is essential for enhancing recovery rates and producing high-purity antimony. As technology advances, the techniques and equipment used in antimony beneficiation will continue to evolve, providing opportunities for improved efficiency and reduced environmental impact. This continuous improvement is vital for meeting the growing global demand for antimony and its derivatives, ensuring a sustainable future for this essential metalloid.
JXSC lab mineral processing equipment manufacturer has more than 38 years of experience in mining processing. We provide various lab mining equipment including gravity-separating equipment for processing minerals such as gold, tin, tungsten, lead, zinc, tantalum, niobium, iron, manganese, silver, titanium-iron, etc. Lab machines include laboratory jaw crusher, hammer crusher, roller crusher, grinding equipment, lab gravity separator, screening, washing equipment, etc. Welcome to consult!