Ilmenite is an oxidized mineral of iron and titanium. It is the raw ore for extracting titanium. Ilmenite has a wide range of uses and can be processed into titanium dioxide powder, various titanium-containing compounds, wear-resistant ceramic materials, magnetic materials, etc. Iron-containing waste residue can also be applied to make flocculants and manganese dioxide. Before bulding a complete mining plant, it will conduct a beneficiation test. How to conduct an ilmenite beneficiation test?
Ilmenite Beneficiation Test Machines
The ilmenite in the raw ore is usually coexisting with magnetite and distributed in magnetite particles or fissures. It is necessary to improve the ore grade through beneficiation technology when obtaining pure titanium ore.
- The ilmenite beneficiation process is relatively complex, involving various beneficiation methods such as gravity separation, magnetic separation, flotation, and electric separation. It needs lots of beneficiation equipment.
- This process includes concentrators that classify ore particles according to particle size. Machines include gravity separation equipment, weak magnetic separators for removing strong-magnetic minerals, strong-magnetic separators for selecting ilmenite, flotation machines for sulfides and fine-grained ilmenite, and electric separators for selecting ilmenite.
Ilmenite Beneficiation Process Flow
Crushing process
The crushing process involves the rock ores rough crushing, which usually uses jaw crushers or cone crushers. These machines have their advantages. Let’s take the jaw crusher as an example. The vibrating feeder transports the large rock ore uniformly to the feeding port of the jaw crusher. The machine body inside is a fixed jaw plate and a moving jaw plate. When starting the operation, the moving jaw plate continuously moves towards the fixed jaw plate, achieving the goal of crushing.
The crushing process will adopt the lab jaw crusher, lab roller crusher, and lab hammer crusher for primary or secondary crushing.
Grinding process
The grinding process involves crushing the material from a jaw crusher, screening it, and then sending it to a ball mill for fine grinding. The ball mill stays on the ground in a high-end and low-end manner. The crushed material enters the ball mill through a high section of the feeding port. The ball mill has two compartments. The material arrives in the first compartment, where steel balls are of different specifications. During the operation of the cylinder, the steel balls are brought to a certain height and then fall to impact the material for the first stage of crushing. After, they enter the second compartment through a partition for further grinding. Then the final material is discharged through a discharge grate to complete the grinding operation.
In this process, we can adopt different lab grinders for grinding.
Grading process
The grading process is relatively simple, mainly using a spiral classifier, which works with a ball mill. Its function is the same as the name, which screens the materials discharged from the ball mill through the spiral classifier. Qualified materials enter the following process, while unqualified materials will return to the ball mill by the spiral classifier for repeated grinding until the materials are qualified.
The grading process equipment usually uses a spiral classifier for separation.
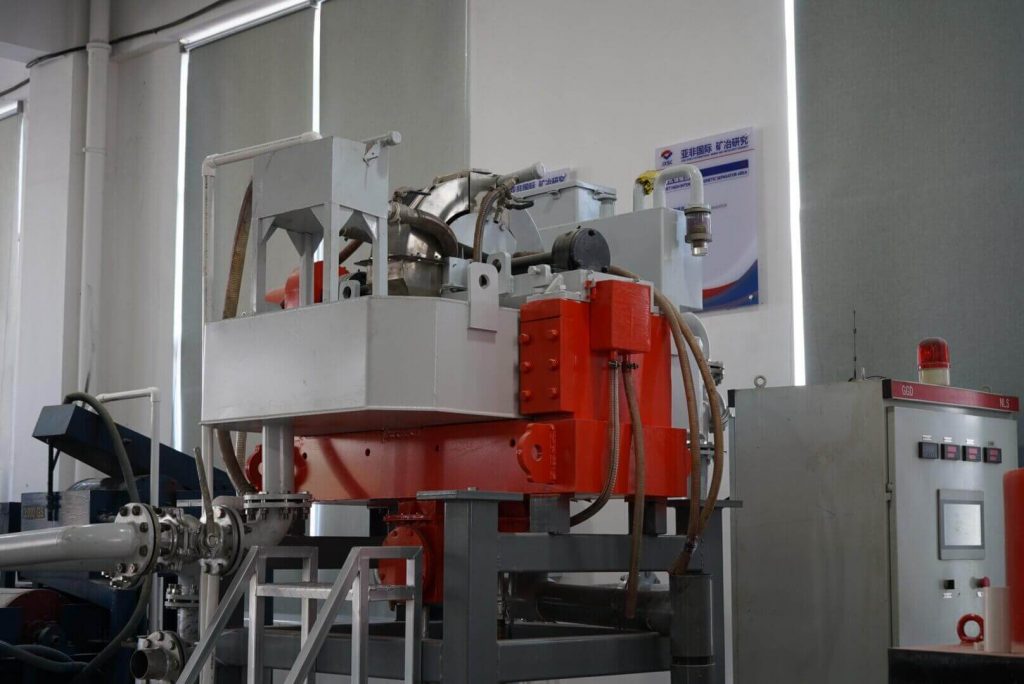
Magnetic separation process
Magnetic separation is an essential process in iron ore selection, which is a crucial step in separating iron and other impurities. The magnetic separator has a large magnetic field. Under the action of the feeding water pipe, the ore particles enter the feeding tank in a loose state. Through the cylinder continuous-rotation to absorb onto the surface of the cylinder. Due to the alternating magnetic poles, magnetic stirring occurs. At this time, non-magnetic minerals fall off during rotation, and the magnet will adhere to the surface of the cylinder to form concentrate. As the rotating cylinder reaches areas with weaker magnetism, it is washed or unloaded by the brush roller to obtain the concentrate.
There are different magnetic separators, roller magnetic separators, 3-disc magnetic separators, etc.
Ilmenite Beneficiation Test Process
The beneficiation process of ilmenite should be designed based on the properties of ilmenite.
There are two major beneficiation processes, “Gravity separation – strong magnetic separation – flotation”Or “gravity separation – strong magnetic separation – electric separation (sulfur removal before separation)”.
Ilmenite Beneficiation Test Process
At the beginning of the process, classify the ore particles by a thickener to distinguish between coarse-grained and fine-grained ores.
- Coarse ore is classified into fine-grained ore and tailings by gravity separation. The cost of gravity is low with small environmental pollution. Remove most useless gangue and soil through equipment such as spiral chutes and shaking tables to obtain enriched concentrate.
- The finely selected ore enters the magnetic separation stage. Ilmenite belongs to weakly magnetic minerals. Under strong magnetic fields, it will separate ilmenite and gangue minerals. Ilmenite is hard to enrich during gravity separation and is re-enriched in this process. Therefore, magnetic separation is an important method in the selection and tailings disposal process.
- The remaining material from the magnetic separation of titanium concentrate is not useless. Use the flotation machine to separate and obtain sulfur concentrate. Fatty acids, oleic acid, and salts are commonly used as flotation collectors for ilmenite. After years of practice, researchers have found that the combination effect of multiple agents is better than a single agent. Therefore, in recent years, the synergistic effect of agents has also been explored.
- After gravity separation, it needs to separate the coarse-grained ore from the titanium concentrate through electrical separation. Especially when it contains ilmenite, rutile, and non-conductive minerals such as quartz. Electrical separation is the final step in the production of titanium concentrate.
- The quality of mineral processing technology directly affects the collection of titanium metal. In the face of different material properties, choosing different process flows and using different beneficiation equipment is necessary to ensure ideal results.
JXSC lab mineral processing equipment manufacturer has more than 38 years of experience in mining processing. We provide various lab mining equipment including gravity-separating equipment for processing minerals such as gold, tin, tungsten, lead, zinc, tantalum, niobium, iron, manganese, silver, titanium-iron, etc. Lab machines include laboratory jaw crusher, hammer crusher, roller crusher, grinding equipment, lab gravity separator, screening, washing equipment, etc. Welcome to consult!