Copper is an essential metal material widely used in various fields such as electrical engineering, construction, and transportation. With technological advancements and increasing market demand, copper production processes have been continuously improved and optimized. This article will delve into the flotation process of copper concentrate and the manufacturing process of electrolytic copper, helping readers comprehensively understand the copper production chain while introducing relevant laboratory mineral processing equipment.
Copper Concentrate Flotation Process
The copper concentrate flotation process is a popular method in copper ore beneficiation. It is primarily aimed at extracting copper concentrate from copper ore and includes several key steps: ore crushing, milling, flotation, and tailings treatment.
1.1 Ore Crushing
The first step in the copper concentrate flotation process is ore crushing. The raw ore has to undergo crushing stages, including primary, secondary, and fine crushing. The purpose of crushing is to control the particle size and impurity content, making it suitable for subsequent milling and flotation processes.
Equipment:
- Jaw Crusher: Used for primary crushing to break large ore into medium-sized particles.
- Hammer Crusher: Used for secondary crushing to further refine the ore.
- Double roller Crusher: Suitable for fine crushing, ensuring the ore reaches the required particle size.
1.2 Grinding
After crushing, the ore enters the grinding stage, which typically employs a ball mill or rod mill for fine grinding. The ore is further ground to a suitable fineness for subsequent flotation.
Equipment:
- Ball Mill: Widely used for ore fine grinding, it grinds the ore into a size suitable for flotation through the impact and friction of the balls.
- Rod Mill: Suitable for processing fine-grained ore and can achieve good grinding results in a shorter time.
1.3 Flotation
The milled ore enters the flotation cell. Here, various reagents, such as collectors and frothers, are added to induce bubble formation on the ore surface, allowing copper minerals to float and separating the copper concentrate.
Equipment:
- Flotation Machine: This machine mixes the milled ore with reagents and generates bubbles; common types include mechanical flotation machines and air flotation machines.
- Laboratory Flotation Cell: determine optimal flotation reagents and process parameters for small-scale tests in the laboratory.
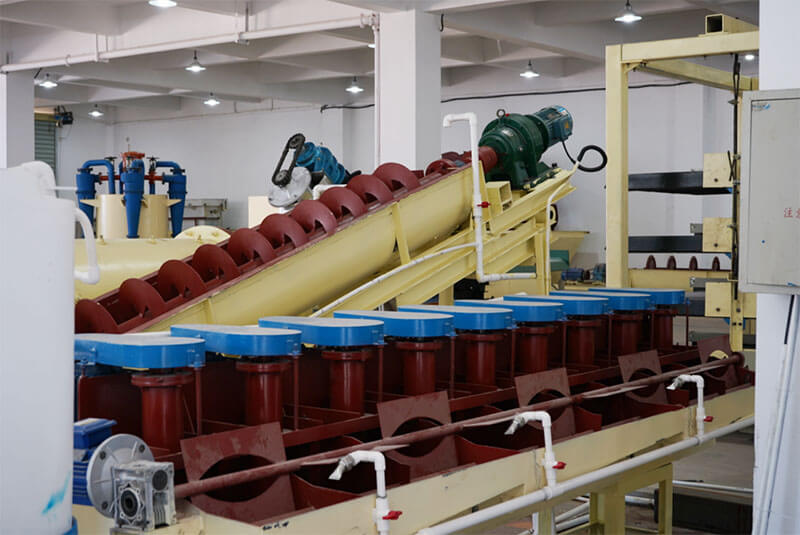
1.4 Tailings Treatment
The waste material produced after flotation refers to tailings. It needs to remove impurities and reduce environmental pollution. Additionally, some copper may remain in the tailings.
Treatment Methods:
- Thickener: concentrate tailings, remove excess water, and recover valuable metals.
- Dehydration Equipment: Use filter presses or dewatering machines to process tailings to reduce their volume and moisture content.
Copper Electrolytic Process
The manufacturing process of electrolytic copper primarily includes raw material preparation, leaching, purification, and electrolysis steps. Each stage requires strict control of process parameters to ensure the quality of the final product.
2.1 Raw Material Preparation
The production of electrolytic copper requires copper-concentrate preparation, sulfuric acid, oxygen, and other raw materials. The copper concentrate is the main raw material containing over 20% copper. Sulfuric acid acts as the electrolyte, while oxygen is used for oxidation reactions. During the raw material preparation process, strict quality testing is necessary to ensure that the purity and quality of the raw materials meet production requirements.
Quality Testing Equipment:
- Chemical Analyzer: Used to detect the chemical composition of copper concentrate, ensuring the copper content meets the requirements.
- Atomic Absorption Spectrometer: measure the content of copper and other elements.
2.2 Leaching
Copper concentrate is mixed with sulfuric acid to undergo a leaching reaction, generating copper sulfate and iron ions. Control reaction temperature and time to ensure sufficient leaching of copper ions. Additionally, to prevent the impact of iron ions and other impurities, appropriate oxidizing agents are added to generate precipitates for removal.
Equipment:
- Leaching Tank: Used for the leaching reaction, usually equipped with temperature control and stirring devices to ensure uniform reactions.
- Stirring Machine: Enhances reaction rates to ensure uniform leaching of copper ions.
2.3 Purification
The leachate contains many impurity ions, such as iron, zinc, and arsenic, necessitating purification treatment. Common purification methods include ion exchange and solvent extraction to remove impurity ions and ensure the purity of the leachate for the subsequent electrolysis process.
Equipment:
- Ion Exchange Column: Used to remove impurity ions from the leachate, enhancing liquid purity.
- Extraction Equipment: solvent extraction columns separate valuable metals from impurities.
2.4 Electrolysis
The purified leachate enters the electrolytic cell, where a direct current is applied for electrolysis. At the cathode, copper ions gain electrons and are reduced to solid copper, depositing on the cathode; at the anode, oxygen ions from the sulfuric acid lose electrons to generate oxygen gas. During the electrolysis process, control parameters such as current and voltage to ensure electrolysis efficiency and product quality.
Equipment:
- Electrolytic Cell: Typically constructed from corrosion-resistant materials to withstand the corrosive nature of the electrolyte.
- DC Power Supply: Provides stable current to ensure smooth electrolysis.
- Current and Voltage Monitoring Instruments: Used to continuously monitor current and voltage, ensuring parameters remain within acceptable ranges during the electrolysis process.
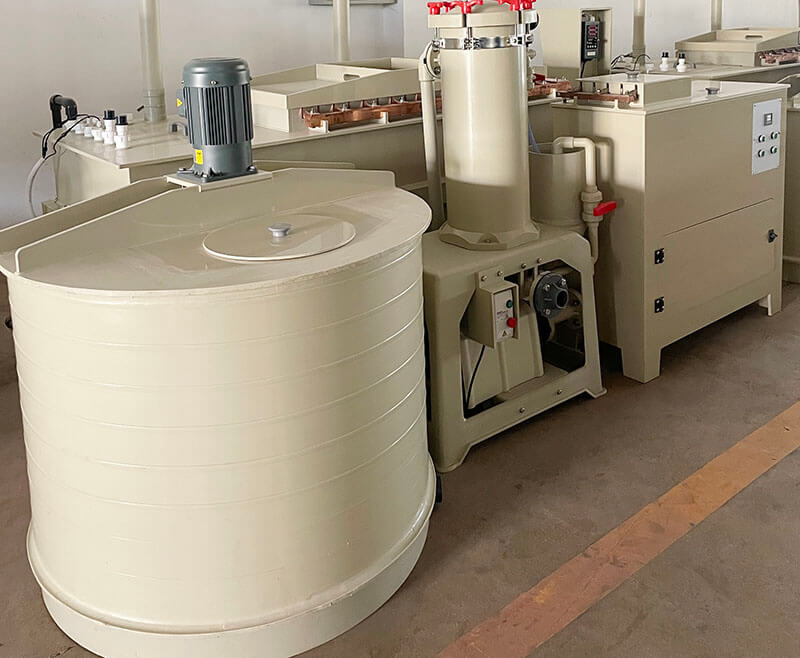
Product Treatment
After electrolysis separation, the solid copper deposited on the cathode must be stripped off and undergo surface treatment and product inspection.
3.1 Surface Treatment
The solid copper on the cathode may be coated with oxides and impurities, necessitating surface treatment. Common methods for surface treatment include mechanical polishing and chemical polishing to enhance the product’s shine.
Equipment:
- Polishing Machine: Used for mechanical polishing to remove surface oxides.
- Chemical Treatment Tank: Used for chemical polishing to improve the copper’s luster.
3.2 Product Inspection
Product quality inspection involves analyzing its chemical composition and physical properties to ensure that it meets standard requirements. Equipment such as spectroscopic analyzers and hardness testers is commonly used for these inspections.
Equipment:
- Spectroscopic Analyzer: Used to detect the purity of copper and the content of impurities, ensuring compliance with industry standards.
- Hardness Tester: Used to measure the physical properties of copper products, ensuring their suitability.
Conclusion
In summary, the copper concentrate flotation process and the electrolytic copper manufacturing method involve multiple steps, each requiring strict control of process parameters and quality indicators to ensure product quality and production efficiency. Furthermore, it is essential to carry out safety management and environmental protection measures during production to ensure the smooth operation of processes.
In the future, we look forward to achieving higher efficiency and lower environmental impacts in the production of electrolytic copper. As an important metal material, every detail of the production process deserves our attention and in-depth exploration. We hope this article provides valuable information to help readers better understand the flotation process of copper concentrate and the manufacturing method of electrolytic copper.
JXSC lab mineral processing equipment manufacturer has more than 38 years of experience in mining processing. We provide various lab mining equipment including gravity-separating equipment for processing minerals such as gold, tin, tungsten, lead, zinc, tantalum, niobium, iron, manganese, silver, titanium-iron, etc. Lab machines include laboratory jaw crusher, hammer crusher, roller crusher, grinding equipment, lab gravity separator, screening, washing equipment, etc. Welcome to consult!