The mining industry faces numerous challenges, especially when extracting and processing valuable ores. One of the most common issues metallurgists encounter is the separation of copper from zinc and lead concentrates. This blog post will guide you in removing copper from zinc and lead, explain the importance of this separation, and detail the lab equipment necessary for effective beneficiation.
Importance of Copper Removal
Copper often occurs in the same ore bodies as zinc and lead. This co-occurrence will complicate the extraction process, leading to several significant challenges:
- Purity of Products: High purity levels are essential in producing zinc and lead products that meet market standards. Any significant copper contamination can lower the quality of the final product, making it less desirable to buyers and potentially leading to financial losses.
- Economic Viability: Removing copper can enhance the overall profitability of the mining operation. Concentrates with higher purity fetch better prices in the market.
- Regulatory Compliance: Many regions have stringent regulations regarding the concentration of metals in final products. Ensuring copper levels are within allowable limits is crucial for compliance with environmental protections and legal standards.
How to Remove Copper from Zinc Lead?
Removing copper from zinc-lead includes several key methods, each with advantages, limitations, and suitability depending on the ore characteristics. Below, we explore the most common techniques:
Froth Flotation
Froth flotation is one of the most widely used methods for separating copper from zinc-lead. This process involves several key steps:
- Grinding: The ore is crushed and ground to liberate the minerals. The goal is to achieve a particle size that allows for optimal separation during flotation.
- Reagent Addition: Chemical reagents—such as collectors, frothers, and modifiers—are added to the slurry to enhance the separation of copper from zinc and lead. Collectors are chemicals that selectively bind to copper minerals, making them hydrophobic, while frothers create stable bubbles that carry these minerals to the surface.
- Air Injection: Air is injected into the flotation cell, creating bubbles that attach to the copper minerals. The hydrophobic copper particles adhere to the bubbles and rise to the surface, forming a froth.
- Concentration: Skim off the froth with copper, while the remaining slurry contains zinc and lead. Further processing may be necessary to refine the copper concentrate.
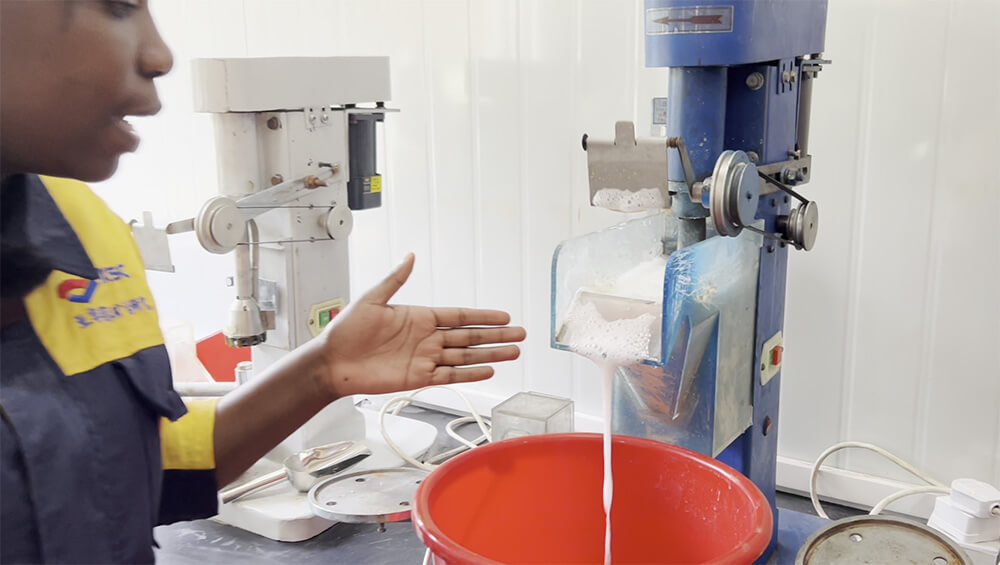
Leaching
Leaching is another effective method for removing copper from zinc-lead concentrates. This technique involves:
- Chemical Treatment: A leaching solution, commonly sulfuric acid, is added to dissolve copper from the concentrate. The choice of leaching agent and conditions (temperature, time, concentration) is critical for maximizing copper recovery.
- Separation: Separate the solution from the solid residue containing zinc and lead by filtration or sedimentation.
- Copper Recovery: Copper can be recovered from the leachate through precipitation, adding chemicals to the solution to form insoluble copper compounds, or solvent extraction, where organic solvents selectively extract copper ions.
Hydrometallurgical Processes
Hydrometallurgy involves using aqueous solutions to extract metals from ores or concentrates. In the case of copper removal, the following steps are generally involved:
- Dissolution: Dissolve copper in an appropriate solvent. This step can include various chemical reactions depending on the composition of the concentrate and the leaching agents.
- Separation: Zinc and lead remain in solid form and can be separated. The remaining solids are often subjected to further processing to recover valuable metals.
- Recovery: Recover the dissolved copper through electrowinning, where an electric current is passed through the solution to deposit copper on cathodes or through precipitation methods.
Pyrometallurgical Processes
For certain ores, pyrometallurgical methods may be suitable. It involves:
- Smelting: Heat the concentrate to high temperatures in the presence of fluxes, which facilitate the separation of metals by altering their melting points and improving the fluidity of the molten mass.
- Refining: The resulting metal is purified, often separating copper from zinc and lead. This step may include further refining processes, such as converting or electrolysis, to achieve desired purity levels.
Laboratory Beneficiation Equipment
To effectively remove copper from zinc-lead, various laboratory equipment is essential. Below is a comprehensive list of the key equipment used in the beneficiation process, along with their functions:
-
Lab Crushers and Grinders
- Purpose: To reduce the size of the ore and liberate the minerals from the surrounding matrix. Effective comminution is crucial for optimizing the subsequent separation processes.
- There are jaw crushers, hammer crushers, and ball mills. Each type of crusher and grinder has specific applications depending on the ore’s hardness and the required particle size.
-
Flotation Cells
- Purpose: To separate copper from zinc and lead using the froth flotation method. The design of the flotation cell significantly impacts the efficiency of copper recovery.
- Features: Must be equipped with efficient agitation and air injection systems to ensure proper mixing and bubble formation. Advanced flotation cells may also include sensors and automation to optimize the flotation process.
-
Leaching Tanks
- Purpose: To facilitate the leaching process by holding the slurry and leaching solution. Proper design ensures effective contact between the ore and leaching agent.
- Design: It should allow for efficient mixing and temperature control. Integrate agitation systems to enhance copper dissolution.
-
Filtration Equipment
- Purpose: To separate solid materials from liquid solutions after leaching. This step is crucial for recovering the remaining metals and ensuring the purity of the leachate.
- Types: Vacuum filters and pressure filters are commonly employed. The choice of filtration equipment can affect recovery rates and the quality of the resulting filtrate.
-
Analytical Equipment
- Purpose: To analyze the composition of concentrates and determine the effectiveness of the separation process. Regular analysis is essential for optimizing the beneficiation process.
- Tools include X-ray fluorescence (XRF) analyzers, atomic absorption spectrophotometers (AAS), and inductively coupled plasma (ICP) systems. These tools provide accurate and timely data on metal concentrations.
-
Electrowinning Cells
- Purpose: To recover copper from leach solutions. It is a critical step in the hydrometallurgical process.
- Functionality: This equipment should provide a controlled environment for copper deposition, ensuring optimal recovery rates and high-quality copper products.
Conclusion
Removing copper from zinc-lead concentrates is critical in mining and metallurgical processes. By employing methods such as froth flotation, leaching, hydrometallurgy, and pyrometallurgy, along with the right laboratory equipment, manufacturers can enhance the quality of their products and comply with regulatory standards.
Investing in the right lab mining equipment is essential for efficient and effective copper removal. As a manufacturer of lab mining equipment, we are committed to providing high-quality solutions to meet the specific needs of the mining industry. We can optimize your beneficiation processes for better efficiency and profitability.
JXSC lab mineral processing equipment manufacturer has more than 38 years of experience in mining processing. We provide various lab mining equipment including gravity-separating equipment for processing minerals such as gold, tin, tungsten, lead, zinc, tantalum, niobium, iron, manganese, silver, titanium-iron, etc. Lab machines include laboratory jaw crusher, hammer crusher, roller crusher, grinding equipment, lab gravity separator, screening, washing equipment, etc. Welcome to consult!