Magnesite is a mineral captured the interest of various industries due to its unique properties and applications. We will explore magnesite, how to beneficiate it, the lab equipment necessary for testing, and the steps to conduct a beneficiation test. This comprehensive guide will provide the knowledge and work with magnesite effectively.
What is Magnesite?
Magnesite is a carbonate mineral with the chemical formula MgCO3. It primarily consists of magnesium carbonate and is typically found in metamorphosed sedimentary rocks. Here are some key points about magnesite:
- Formation: Magnesite is formed by altering ultramafic rocks, like peridotite and serpentine.
Appearance: It usually appears as white or light-colored crystalline masses, but it can also occur in shades of grey, brown, or green. - Properties: Magnesite is known for its high melting point, low thermal conductivity, and resistance to chemical attack, making it valuable in various applications.
- Uses: It is used primarily in refractory materials, fertilizers, the steel industry, and the manufacturing of magnesium compounds.
How to Beneficiate Magnesite?
Beneficiation is the process of improving the economic value of a mineral by removing impurities. Magnesite beneficiation involves several steps to enhance its purity and quality for industrial applications.
Steps in Magnesite Beneficiation:
Crushing and Grinding:
Crush magnesite ore to liberate the ore from the surrounding material.
Grinding reduces the particle size, increasing the surface area for further processing.
Screening:
Screen the crushed and ground material to separate fine particles from coarse ones.
This step helps in optimizing the subsequent processes by removing undesired sizes.
Flotation:
Flotation is a common separation technique used for magnesite beneficiation.
It involves adding chemical reagents to create a froth that selectively separates magnesite from other minerals based on their surface properties.
Magnetic Separation:
If the magnesite contains iron or other magnetic minerals, use magnetic separation to separate the iron.
This technique utilizes magnets to separate magnetic impurities, enhancing the purity of magnesite.
Calcination (optional):
In some cases, calcination converts magnesite into magnesia (MgO).
This step involves heating magnesite to high temperatures to drive off carbon dioxide.
Lab Magnesite Beneficiation Equipment
Conducting magnesite beneficiation tests requires different laboratory equipment. Here’s a detailed look at essential equipment, including their functions and specifications:
Crushing and Grinding Equipment
- Function: Reduces the size of large magnesite chunks to a manageable size.
- Features: Typically has a crushing ratio of 6:1 to 8:1 and can handle materials with a maximum feed size of about 150 mm.
- Specifications: Available in various sizes, a laboratory model might have a capacity of 1-2 tons per hour.
- Ball Mill or Rod Mill:
- Function: Further reduces the particle size after crushing.
- Features: Provides efficient grinding and can be operated in batch or continuous mode.
- Specifications: The capacity of a laboratory ball mill is 0.5 to 20 kg per batch and can achieve particle sizes down to 45 microns.
Screening Equipment
- Vibrating Screens:
- Function: Separates particles based on size after crushing and grinding.
- Features: efficient stratification of materials.
- Specifications: Laboratory models have multiple decks and process 1-2 tons of material per hour.
Flotation Equipment
- Flotation Cell:
- Function: Conducts flotation tests to separate magnesite from impurities.
- Features: Equipped with an impeller for agitation and a froth collection system.
- Specifications: Laboratory flotation cells typically have a 1-5 liter volume and can be operated at varying speeds and airflow rates.
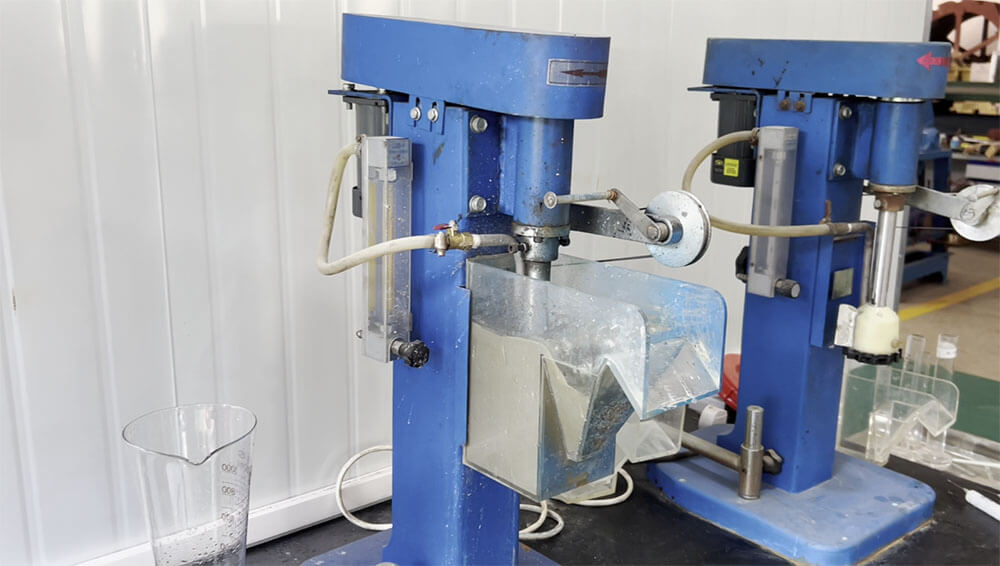
4. Magnetic Separation Equipment
- Magnetic Separator:
- Function: Removes magnetic impurities from the magnesite.
- Features: For wet or dry separation, depending on the requirements.
- Specifications: Laboratory magnetic separators may have a capacity of 0.5 to 5 tons per hour and can achieve magnetic field strengths of 1,000 to 20,000 gauss.
5. Analytical Equipment
- X-Ray Fluorescence (XRF) Analyzer:
- Function: Determines the chemical composition of the magnesite.
- Features: Non-destructive analysis and provides rapid results.
- Specifications: Compact models for laboratory use can analyze samples in concentrations and provide results in minutes.
- Scanning Electron Microscope (SEM)
- Function: Offers detailed analysis of the mineral surface and morphology.
- Features: Provides high-resolution images and elemental analysis.
- Specifications: Laboratory SEMs can achieve magnifications of up to 1,000,000x and can analyze samples in the nanometer range.
-
Miscellaneous Equipment
- pH Meter:
- Function: Monitors and adjusts the pH during flotation to optimize the process.
- Specifications: Laboratory pH meters are typically portable and can provide accurate readings within 0-14 pH.
- Weighing Scales:
- Function: For accurate measurement of samples and reagents.
- Specifications: Analytical balances can measure samples with precision down to 0.0001 grams.
Lab Magnesite Beneficiation Test
The beneficiation test involves a systematic approach to ensure accurate and reproducible results. Here’s a step-by-step guide:
Step 1: Sample Preparation
- Collect Samples: Obtain representative samples of magnesite ore to ensure the test results indicate the whole.
- Crushing and Grinding: Use a jaw crusher followed by a ball mill to crush and grind the samples to the desired particle size.
Step 2: Screening
- Screen the Ground Material: Utilize vibrating screens to separate the material into different sizes.
- Select Appropriate Fractions: Choose the size fractions that are most suitable for flotation and further testing.
Step 3: Flotation Testing
- Prepare the Flotation Slurry: Mix the selected size fraction with water and add flotation reagents (collectors, frothers).
- Conduct Flotation: Transfer the slurry to the flotation cell and adjust the parameters (pH, temperature, stirring speed).
- Collect Froth: After a predetermined time, collect the froth that contains the floated magnesite.
Step 4: Magnetic Separation
- Process the Concentrate: If necessary, send the collected froth through a magnetic separator to remove any remaining impurities.
- Analyze the Results: Collect both the magnetic and non-magnetic fractions for analysis.
Step 5: Analysis and Reporting
- Chemical Analysis: Use XRF to determine the chemical composition of the magnesite concentrate.
- Evaluate Results: Assess the recovery rate and purity of the beneficiated magnesite.
- Documentation: Document all findings, including the methods used, results obtained, and any observations made during the testing process.
Conclusion
Understanding magnesite and its beneficiation process is crucial for industries that rely on this valuable mineral. By following the steps outlined in this blog, manufacturers can optimize their processes, improve product quality, and enhance their operational efficiency.
Whether you want to set up a lab for magnesite beneficiation testing or improve your existing processes, having the right knowledge and equipment is essential.
JXSC lab mineral processing equipment manufacturer has more than 38 years of experience in mining processing. We provide various lab mining equipment including gravity-separating equipment for processing minerals such as gold, tin, tungsten, lead, zinc, tantalum, niobium, iron, manganese, silver, titanium-iron, etc. Lab machines include laboratory jaw crusher, hammer crusher, roller crusher, grinding equipment, lab gravity separator, screening, washing equipment, etc. Welcome to consult!