Fluorite, calcium fluoride (CaF₂), is a vital industrial mineral with applications in metallurgy, chemical production, and construction. As global demand for fluorite increases, optimizing beneficiation techniques is essential for improving recovery rates and ensuring sustainable resource management. Laboratory-scale beneficiation plays a critical role in developing and refining these techniques. This article explores the equipment used in laboratory fluorite beneficiation and outlines the associated processes.
I. Laboratory Fluorite Beneficiation Equipment
Laboratory fluorite beneficiation involves specialized equipment designed to process and analyze fluorite ores efficiently. The equipment includes crushing machines, grinding mills, classification devices, flotation machines, and analytical instruments.
Lab Crushing Equipment
Crushing is the first step in the beneficiation process, aiming to reduce the size of the ore so it can be further processed. Laboratory crushing equipment includes:
- Jaw Crusher: This device is suitable for primary crushing due to its simple design and reliable operation. It effectively crushes mineral ores in small-scale laboratory tests.
- Hammer Crusher: This hammer crusher is suitable for brittle materials and can efficiently crush fluorite ore into smaller particles, facilitating subsequent grinding processes.
Lab Grinding Equipment
Grinding is crucial for further reducing the size of the crushed ore, making it easier to separate fluorite from gangue minerals. Laboratory grinding equipment includes:
- Ball Mill: The ball mill is the most commonly used grinding device in
- Rod Mill: Typically used for coarser grinding, rod mills are effective for processing hard ores and enhancing grinding efficiency.
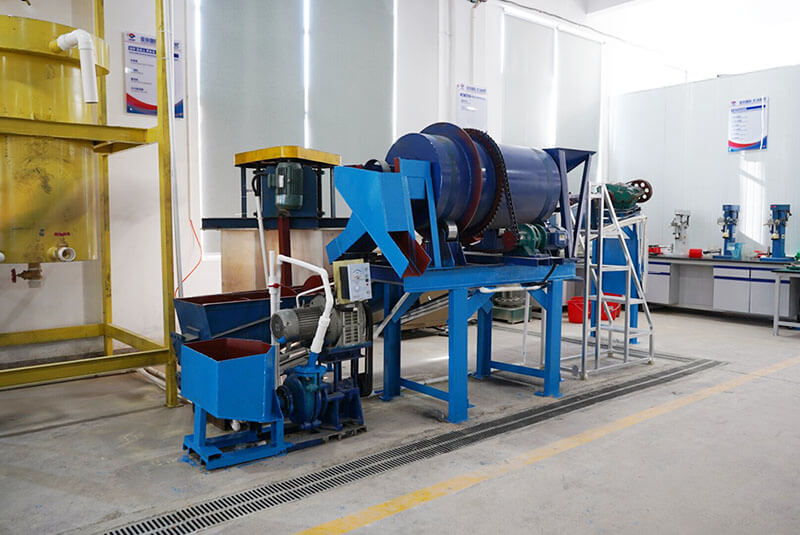
Classification Equipment
Classification equipment separates ground material based on particle size, ensuring that only the appropriately sized particles proceed to flotation. Laboratory classification devices include:
- Spiral Classifier: This equipment utilizes differences in settling rates of particles in a slurry to separate them by size. It is suitable for larger particles in laboratory processes.
- Laboratory Screening Equipment: This equipment, such as vibrating screens, quickly separates various particle sizes, providing immediate feedback on the grinding process.
Flotation Equipment
Flotation is the essential process in fluorite beneficiation, allowing for the selective separation of fluorite from unwanted minerals. Laboratory flotation equipment typically includes:
- Flotation Cell: This device is the primary equipment used in flotation experiments, which allows the addition of reagents and control of operational conditions. It is suitable for testing various minerals with different flotation parameters.
- Mini Flotation Machine: Ideal for small-scale experiments, these machines enable researchers to conduct flotation tests with minimal sample sizes and provide accurate data on flotation performance.
Analytical Equipment
To evaluate the effectiveness of the beneficiation process, analytical equipment is essential for determining the chemical composition and mineralogy of processed samples. Analytical devices include:
- X-Ray Fluorescence Spectrometer (XRF): This instrument enables rapid analysis of the chemical composition of fluorite samples, providing insights into the purity and quality of the product.
- Scanning Electron Microscope (SEM): SEM allows for detailed examination of mineral structure and morphology, helping researchers understand the flotation behavior of fluorite and associated minerals.
II. Laboratory Fluorite Beneficiation Process
The laboratory fluorite beneficiation process typically involves several stages, including crushing, grinding, classification, flotation, dewatering, and analysis.
Ore Crushing
The process begins with crushing the fluorite ore to get the material size to approximately 10-20 mm. Using a jaw or hammer crusher to get the finer materials. The goal is to create a uniform particle size for efficient processes in subsequent steps.
Grinding
The crushed ore enters a ball mill or rod mill. This process may employ either wet or dry grinding methods. Wet grinding is often preferred in laboratory settings, as it promotes better mineral dispersion and enhances flotation performance. Grinding time and periodic sampling are essential to ensure the desired particle size.
Classification
After grinding, the ore slurry passes through classification equipment to separate particles by size. The spiral classifier or laboratory screening allows for the effective separation of coarser particles from finer ones. This step is crucial for optimizing the flotation process.
Flotation
Pour the classified slurry into the flotation cell. In this step, flotation reagents, including collectors, frothers, and depressants, are added to enhance the separation of fluorite from gangue minerals. The flotation process generates air bubbles that attach to fluorite particles, allowing them to float to the surface.
Dewatering
After flotation, the mineral concentrate requires dewatering to reduce moisture content and improve handling. Laboratory-scale dewatering can be achieved by using a filter press or centrifuge. This step enhances the quality of the final product by concentrating the fluorite and minimizing impurities.
Analysis
Finally, the dewatered fluorite concentrate is analyzed to determine its chemical composition and recovery rate. XRF analysis provides quantitative data on the purity of the fluorite, while SEM can give insights into the morphology and surface characteristics of the concentrate. These analyses are crucial for evaluating the effectiveness of the beneficiation process and guiding further optimization.
III. Challenges and Future Directions in Laboratory Beneficiation
While laboratory beneficiation techniques for fluorite are essential for research and development, they face several challenges:
1. Technical Challenges
- Equipment Limitations: Laboratory equipment is often smaller and less powerful than industrial counterparts, which may affect the scalability of results. Limited capacity can lead to variability in results if not carefully controlled.
- Sample Representativeness: The samples used in laboratory experiments may not accurately represent the entire ore body, potentially leading to misleading conclusions about the overall beneficiation process.
- Reagent Optimization: Different ore types respond variably to flotation reagents. Finding the optimal combination of reagents for specific fluorite ores can be challenging and requires extensive testing.
2. Future Development Directions
To address these challenges, the future of laboratory fluorite beneficiation will likely focus on several key areas:
- Automation and Control: Implementing automated systems for monitoring and controlling laboratory processes can enhance reproducibility and efficiency, allowing for more precise experimentation.
- Development of Eco-Friendly Reagents: Research into environmentally friendly flotation reagents can lead to more sustainable beneficiation processes, reducing the ecological footprint of fluorite mining.
- Integration of Advanced Technologies: Utilizing advanced technologies, such as machine learning and artificial intelligence, can help optimize the beneficiation process by predicting outcomes based on historical data and real-time monitoring.
Conclusion
Laboratory fluorite beneficiation equipment and processes are vital in optimizing fluorite extraction techniques. Using appropriate crushing, grinding, classification, flotation, and analytical equipment, researchers can gain valuable insights into the efficiency of different beneficiation methods. As the demand for fluorite continues to grow, overcoming the challenges faced in laboratory settings and advancing research in this field will be essential for improving recovery rates and ensuring sustainable resource management. Through innovation and technology, the future of fluorite beneficiation looks promising, paving the way for more efficient and environmentally friendly practices.
JXSC lab mineral processing equipment manufacturer has more than 38 years of experience in mining processing. We provide various lab mining equipment including gravity-separating equipment for processing minerals such as gold, tin, tungsten, lead, zinc, tantalum, niobium, iron, manganese, silver, titanium-iron, etc. Lab machines include laboratory jaw crusher, hammer crusher, roller crusher, grinding equipment, lab gravity separator, screening, washing equipment, etc. Welcome to consult!