Phosphorus is an essential element that is critical in various biological and industrial processes. As a manufacturer of lab mining equipment, understanding phosphorus—its characteristics, sources, and the processes involved in its beneficiation—is vital. This blog will delve into what phosphorus is, how it is beneficiated, the lab equipment necessary for conducting beneficiation tests, and the steps to perform these tests effectively.
What is Phosphorus?
Phosphorus is a non-metallic chemical element with the symbol P and atomic number 15. It is a vital nutrient for plants and animals, playing a crucial role in biological processes such as energy transfer, photosynthesis, and the formation of DNA and RNA. Phosphorus is found in several forms, each with unique properties and applications.
Types of Phosphorus
White Phosphorus
Highly reactive and luminous, it is primarily used in fertilizers, pesticides, and industrial applications. White phosphorus is known for its ability to ignite spontaneously in air, making it both useful and hazardous.
Red Phosphorus
This form is more stable than white phosphorus. Red phosphorus does not ignite easily, making it safer to handle than its white counterpart.
Black Phosphorus
The least reactive form, black phosphorus, is used in electronic applications and as a lubricant. Its layered structure allows it to conduct electricity, making it valuable in the semiconductor industry.
How to Beneficiate Phosphorus?
Beneficiation refers to improving a mineral’s economic value by removing impurities or enhancing its properties. It involves several steps to increase phosphorus concentration.
Steps in Phosphorus Beneficiation
Crushing and Grinding:
The first step in the beneficiation process is crushing and grinding. It is essential for liberating the phosphorus-bearing minerals from the surrounding matrix.
Equipment Used: Jaw crushers are typically employed to perform the initial crushing, followed by ball mills for grinding the material to a finer particle size.
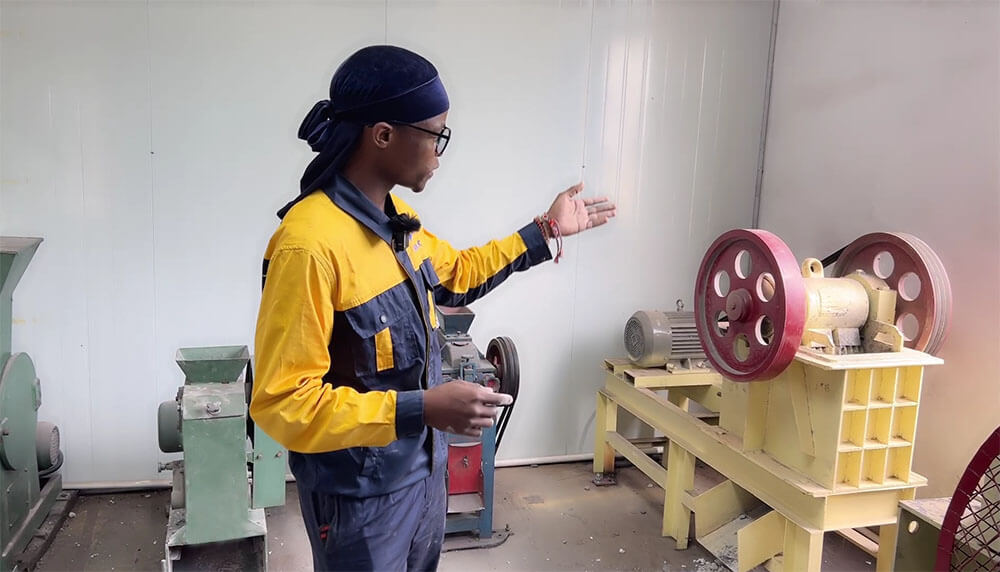
Screening:
After grinding, screen the material to separate finer particles from coarser ones. Effective screening allows for improved separation of valuable phosphorus minerals from gangue materials.
Equipment Used: Vibrating screens and sieves ensure proper classification based on particle size.
Flotation:
Flotation is a critical step. Add chemicals to the slurry to selectively separate phosphorus from other minerals. This process relies on the differences in surface properties of minerals.
Equipment Used: Flotation cells introduce air bubbles into the slurry and allow for the attachment of hydrophobic mineral particles to the bubbles, which rise to the surface and form a froth.
Magnetic Separation:
Following flotation, magnetic separation removes any ferrous or paramagnetic minerals that could contaminate the phosphorus concentrate.
Equipment Used: Magnetic separators to achieve this separation, ensuring a higher purity of the final product.
Thickening and Filtration:
After flotation and magnetic separation, use a thickener to concentrate, making subsequent handling easier.
Equipment Used: Thickeners consolidate the slurry, while filter presses remove excess water and produce a drier concentrate.
Drying:
The final step involves reducing the moisture content of the phosphorus concentrate to prepare it for storage and transport.
Equipment Used: Dryers, including rotary kilns and drying ovens, are employed to achieve the desired moisture level.
Important Considerations in the Beneficiation Process
- Reagent Selection: The effectiveness of the flotation process is heavily influenced by the choice of reagents. Selecting the appropriate collectors, frothers, and modifiers is essential for maximizing phosphorus recovery.
- pH Control: Maintaining an optimal pH during flotation is crucial for enhancing the separation efficiency of phosphorus from other minerals. Small pH adjustments can lead to significant changes in mineral behavior.
- Environmental Impact: It is vital to consider the environmental implications of phosphorus beneficiation. Implementing eco-friendly practices and technologies can help minimize waste and pollution, contributing to sustainable mining operations.
Lab Phosphorus Beneficiation Equipment for Tests
To effectively conduct phosphorus beneficiation tests, various lab equipment is required. Here’s a comprehensive list of essential equipment:
Jaw Crusher
Used for the initial crushing of phosphate rock, reducing it to manageable sizes for further processing.
Ball Mill
It is the key equipment for grinding the material to liberate phosphorus-bearing minerals from the matrix.
Vibrating Screen
Separates different particle sizes, allowing for the classification of materials before flotation.
Flotation Cell
The core of the flotation process is to separate phosphorus from other minerals through chemical treatment and air introduction.
Magnetic Separator
Essential for removing unwanted magnetic minerals from the concentrate, ensuring higher purity of phosphorus-containing products.
Thickener
Concentrates the slurry by allowing solids to settle, thus reducing water content for easier handling.
Filter Press
Utilized for dewatering the concentrate, removing excess water to produce a drier product.
Drying Oven or Rotary Dryer
Reduces moisture content to prepare the final product for analysis and market readiness.
pH Meter and Reagent Dispensers
Monitoring and adjusting the pH during the flotation process to optimize recovery.
How to Conduct Phosphorus Beneficiation Tests?
Conducting phosphorus beneficiation tests is a systematic process that involves careful planning and execution. Below is a detailed step-by-step guide:
Step 1: Sample Preparation
Collect Samples: Obtain representative phosphate samples to ensure the test results apply to real-world conditions.
Crush and Grind: Utilize a jaw crusher followed by a ball mill to reduce the sample size to the desired fineness for the liberation of phosphorus-bearing minerals.
Step 2: Screening
Separate Particles: Use a vibrating screen to classify the ground material based on particle size, ensuring the appropriate fractions are available for flotation.
Step 3: Conduct Flotation Tests
Prepare Flotation Cell: Fill the flotation cell with the ground slurry, ensuring a proper ratio of solids to liquid.
Add Reagents: Introduce the selected flotation reagents, adjusting the pH as necessary to optimize conditions for phosphorus recovery.
Agitate the Mixture: Use an agitator to promote the interaction between the particles and the reagents, enhancing the flotation process.
Collect Froth: Skim off the froth that contains concentrated phosphorus, ensuring minimal loss of valuable material.
Step 4: Magnetic Separation
Run the Magnetic Separator: Pass the froth concentrate through a magnetic separator to remove any magnetic impurities that could affect the quality of the final product.
Step 5: Thickening and Filtration
Thicken the Slurry: Use a thickener to consolidate the slurry, facilitating easier handling and preparation for filtration.
Filter the Concentrate: Employ a filter press to effectively remove excess water from the concentrate, enhancing its dryness.
Step 6: Drying
Dry the Product: Use a drying oven or rotary dryer to reduce the moisture content of the phosphorus concentrate, preparing it for further analysis and market distribution.
Step 7: Analysis
Assess Phosphorus Content: Conduct chemical analysis on the final product to determine the recovery rate and purity of the phosphorus concentrate, providing valuable data for process optimization.
Conclusion
Phosphorus is a crucial element for life and agriculture, making its beneficiation an important process in the mining industry.
As a manufacturer of lab mining equipment, providing the right tools and technologies for phosphorus beneficiation tests supports efficient mining practices and contributes to sustainable resource management. Continuous research and development in this field will help improve the recovery rates and environmental impact of phosphorus processing, ensuring that future generations can benefit from this essential element.
JXSC lab mineral processing equipment manufacturer has more than 38 years of experience in mining processing. We provide various lab mining equipment including gravity-separating equipment for processing minerals such as gold, tin, tungsten, lead, zinc, tantalum, niobium, iron, manganese, silver, titanium-iron, etc. Lab machines include laboratory jaw crusher, hammer crusher, roller crusher, grinding equipment, lab gravity separator, screening, washing equipment, etc. Welcome to consult!