Rutile is a crucial titanium mineral primarily composed of titanium dioxide (TiO₂). It has wide applications in various industries, including aerospace, automotive, and pigment manufacturing. Rutile is valued for its high refractive index and ability to withstand high temperatures, which makes it an essential raw material for producing titanium dioxide pigments, titanium metal, and various titanium alloys. Rutile beneficiation is necessary to enhance its purity and concentration for these applications. This blog post will explore the methods and steps in rutile mining beneficiation, the laboratory tests, and the equipment necessary for effective processing.
Understanding Rutile
Rutile usually exists alongside other minerals like ilmenite, zircon, and monazite. It typically occurs in igneous and metamorphic rocks and sedimentary deposits. Its high density and resistance to weathering make it a valuable resource. The primary goal of rutile beneficiation is to separate it from these associated minerals to produce a high-quality concentrate that meets the particular standards required for industrial applications.
Rutile Mining Beneficiation Methods
The beneficiation process for tin ore involves several steps, including crushing, grinding, concentration, and refining. Let’s delve into the specific process steps for rock-type and alluvial tin ores, highlighting their unique characteristics.
1. Crushing and Grinding
The first step in the beneficiation process is crushing the ore to liberate rutile from the gangue. These are the crushing machines for it.
- Jaw Crushers: The jaw crushers are the initial size reduction of larger pieces of ore. They crush the ore into smaller fragments, making it easier to process in subsequent stages.
- Cone Crushers: Often used for secondary crushing, cone crushers provide a finer particle size, which is crucial for liberating rutile from other minerals.
After crushing, the material is ground to a finer size using:
- Ball Mills: The ball mills grinding achieves a fine particle size and liberates the rutile from the surrounding gangue materials. The grinding process increases the surface area of the particles, facilitating better separation in subsequent processes.
2. Gravity Separation
Gravity separation is one of the most effective methods for rutile beneficiation due to its high density. This method exploits the density differences between rutile and gangue minerals. Equipment used in gravity separation includes:
- Jig separator: Jig separators separate heavy minerals efficiently from lighter ones based on density differences. They are suitable for both batch and continuous operations.
- Spirals: Spiral concentrators utilize gravity and centrifugal force to separate minerals based on density. Rutile is collected in the inner part of the spiral, while lighter gangue materials are carried away.
- Shaking Tables: These tables use gravity and motion to separate minerals. The shaking action helps to stratify the particles according to their density, allowing for the recovery of a concentrated rutile product.
3. Magnetic Separation
Rutile is non-magnetic, allowing for the removal of magnetic impurities like ilmenite and magnetite through magnetic separation. The equipment for this method includes:
- Wet Magnetic Separators: Separate magnetic minerals from non-magnetic ones, and retain the non-magnetic rutile while the magnetic impurities are removed.
- Dry Magnetic Separators: These magnetic separators require drying before use. They are efficient for materials with significant differences in magnetic properties.
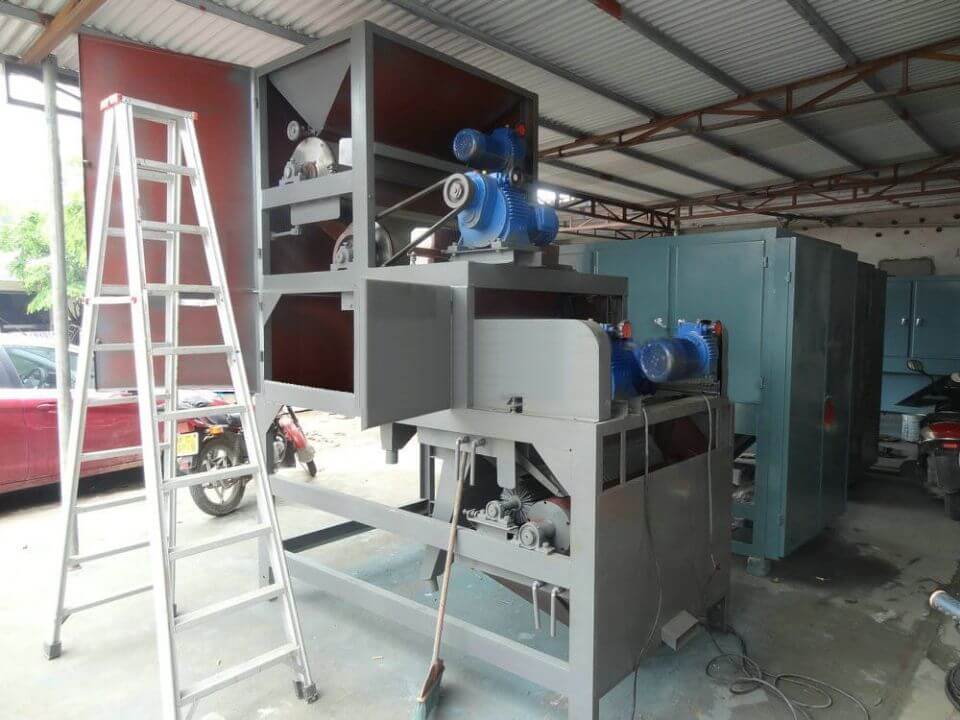
4. Electrostatic Separation
Electrostatic separation is another effective method for purifying rutile. It separates rutile from non-conductive minerals based on electrical conductivity differences. This technique is effective for producing high-purity rutile concentrates. The steps involved are:
- Charging Particles: In an electrostatic separator, discharge particles using high-voltage electrodes. Rutile, a conductive mineral, responds differently to the electric field than non-conductive gangue minerals.
- Separation: The charged particles go to an electric field, which causes them to separate based on their charge and conductivity.
5. Flotation
Flotation is a chemical process for purifying rutile. This method involves the additional reagents to create a frothy layer on the surface of the slurry and float the rutile away from the gangue. Key steps include:
- Adjusting pH: The pH of the slurry is adjusted to optimize the flotation process to enhance the hydrophobicity of rutile and improve its recovery.
- Using Collectors and Frothers: Collectors are chemicals that selectively bind to rutile, making it hydrophobic. Frothers help to stabilize the froth, allowing for better separation during the flotation process.
6. Chemical Treatment (Optional)
This needs chemical treatments such as acid leaching for higher purity. This process involves:
- Leaching with Acid: Acid solutions dissolve impurities, such as iron and other trace elements, that can affect the quality of rutile. The treated material is then washed and neutralized to remove any residual acid.
Lab Rutile Beneficiation Tests
Importance of Lab Testing
Conducting laboratory tests is critical for optimizing the beneficiation process. These tests help clients understand the ore’s characteristics and determine the most effective beneficiation methods. Lab tests also provide valuable data for scaling up processes for commercial production.
Steps for Lab Rutile Beneficiation Testing
- Sample Collection: Collect representative samples of rutile ore for testing to ensure the results indicate the entire deposit.
- Crushing and Grinding: Process the samples through crushing and grinding to achieve the desired particle size, typically ranging from 100 to 200 microns.
- Conduct Beneficiation Tests: Perform gravity separation, magnetic separation, electrostatic separation, and flotation tests. Monitor each method carefully to assess its effectiveness.
- Analyze Results: Evaluate the grade and recovery of rutile from the tests. It involves measuring the concentration of TiO₂ in the final product and comparing it to the initial ore grade.
- Report Generation: Compile a detailed report on the findings, including recommendations for optimal processing methods based on the test results. This report can guide further development and implementation of the beneficiation process.
Equipment Needed for Rutile Beneficiation
Essential Laboratory Equipment
The following equipment is typically required to carry out rutile beneficiation tests.
- Jaw Crusher: For initial crushing of the ore to liberate rutile.
- Ball Mill: Grinding the crushed material to powder to enhance the liberation of minerals.
- Laboratory Jigs: For conducting gravity separation tests on a small scale.
- Shaking Table: Concentrate the rutile and separate it from lighter gangue materials.
- Magnetic Separator: Remove magnetic impurities from the rutile concentrate.
- Electrostatic Separator: For further purification of rutile based on electrical conductivity.
- Flotation Cell: Conducting flotation tests and achieving higher purity levels.
- Sample Analysis Equipment: Test the grade of the concentrates, including X-ray fluorescence (XRF) analyzers and other analytical instruments.
Conclusion
Rutile mining beneficiation is a multifaceted process that requires careful planning and execution. By utilizing effective methods and laboratory tests, manufacturers can produce high-purity rutile concentrates essential for various industrial applications. At [Your Company Name], we specialize in providing high-quality lab mining equipment and comprehensive beneficiation testing services, complete with detailed reports to guide your operations.
Investing in effective beneficiation methods enhances the quality of the rutile produced and contributes to more sustainable mining practices by reducing waste and optimizing resource use.
JXSC lab mineral processing equipment manufacturer has more than 38 years of experience in mining processing. We provide various lab mining equipment including gravity-separating equipment for processing minerals such as gold, tin, tungsten, lead, zinc, tantalum, niobium, iron, manganese, silver, titanium-iron, etc. Lab machines include laboratory jaw crusher, hammer crusher, roller crusher, grinding equipment, lab gravity separator, screening, washing equipment, etc. Welcome to consult!