Cobalt is a crucial metal that plays a significant role in various industries, particularly in producing batteries, alloys, and catalysts. As demand for cobalt continues to rise, especially with the growth of electric vehicles and renewable energy storage, understanding its properties, extraction, and processing becomes increasingly important. This blog will explore cobalt, how to beneficiate it, and the lab equipment for cobalt beneficiation testing.
Cobalt Introduction
Cobalt is a transition metal with the chemical symbol Co and atomic number 27. It is known for its distinctive blue color and exhibits several noteworthy properties that make it valuable in various applications.
Key Properties of Cobalt
- High Melting Point: Cobalt’s melting point is about 1,495 °C (2,723 °F), making it suitable for high-temperature applications.
- Corrosion Resistance: It is resistant to oxidation and corrosion, which enhances its durability in various environments.
Magnetic Properties: It is ferromagnetic. - Alloying Element: Cobalt is an alloying element to improve hardness and temperature resistance.
Applications of Cobalt
It is widely used in rechargeable lithium-ion batteries. Cobalt is essential for electric vehicles (EVs), smartphones, laptops, and other electronic devices. It is also critical in superalloys production for jet engines, cutting tools, and wear-resistant materials. Additionally, cobalt is utilized in petroleum refining and chemical production, making it an integral component of modern industry.
How to Beneficiate Cobalt?
Beneficiation refers to improving the economic value of ore by removing impurities and increasing the concentration of the mineral. For cobalt, this process is crucial to ensure efficient extraction and production. The methods in cobalt beneficiation can vary based on the ore type and composition.
Crushing and Grinding
The first step involves crushing the ore to liberate cobalt minerals from gangue materials. It usually uses jaw crushers and ball mills. The goal is to reduce the ore size to facilitate further processing.
Concentration
There are various methods concentrate cobalt after crushing:
- Froth Flotation: This is the most common method for cobalt concentration. It involves adding chemicals to create a froth that selectively binds to cobalt minerals, separate it from the gangue. The process relies on the differences in surface properties between cobalt and other minerals.
- Magnetic Separation: When cobalt is associated with magnetic minerals, the magnetic separation method isolates cobalt-bearing minerals. This method is particularly effective when cobalt is present in sulfide ores.
- Gravity Separation: Techniques such as jigging and shaking tables can separate cobalt from other minerals based on density differences. This method is more common in primary cobalt ores.
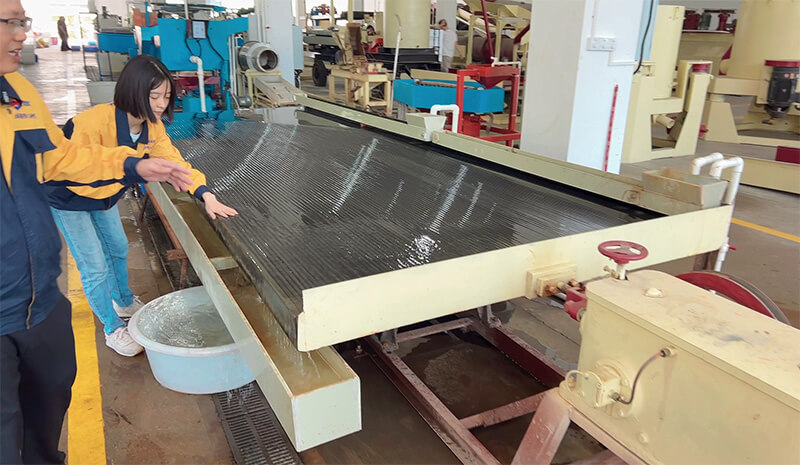
3. Hydrometallurgical Processing
Following concentration, use hydrometallurgical methods to extract cobalt from its ores. It involves using solvents to dissolve cobalt, and recovered through various means, including precipitation or solvent extraction. This step is crucial for obtaining high-purity cobalt suitable for industrial applications.
4. Purification
The final step is to purify the cobalt to obtain high-purity cobalt products. It may involve electrowinning or additional chemical treatments to remove impurities. The cobalt is critical for its applications in batteries and alloys, where even minor impurities can affect performance.
Challenges in Cobalt Beneficiation
While cobalt beneficiation is essential for efficient production, it comes with its own set of challenges:
- Complex Ore Composition: Cobalt often occurs in complex ores with other metals, making separation challenging. The nickel, copper, and iron can complicate processing and lead to lower recovery rates.
- Environmental Concerns: The chemicals in beneficiation processes raise safety issues. The potential for chemical spills and wastewater contamination necessitates careful management and adherence to regulations.
- Economic Viability: The cost of beneficiation must be weighed against the market price of cobalt. Fluctuations in cobalt prices can impact the feasibility of some beneficiation methods.
Lab Cobalt Beneficiation Testing Equipment
When conducting cobalt beneficiation testing, having the right lab equipment is essential to ensure accurate results and efficient processing. Here’s a list of the equipment commonly used in cobalt beneficiation testing
Lab Crushing Equipment
- Lab Jaw Crushers: Used for primary crushing of the ore. This equipment prepares the ore for subsequent grinding and concentration processes.
- Roll Crushers: Alternative to jaw crushers for further size reduction, especially for softer ores.
Lab Grinding Mills
- Lab Ball Mills: The grinding process helps achieve the desired particle size for effective separation.
- Rod Mills: useful for coarse grinding. Rod mills can be advantageous for specific ore types.
Lab Separation Equipment
- Lab Froth Flotation Cells: Separate cobalt from other minerals. Flotation cells vary in size and design to accommodate different scales of operation.
- Magnetic Separators: For separating magnetic minerals from cobalt-containing ores.
- Lab Shaking Tables: Gravity separation equipment is effective in concentrating cobalt. Shaking tables rely on the differences in density and particle size to achieve separation.
Leaching Equipment
- Leaching Tanks: For hydrometallurgical processing, where ore is treated with chemicals to extract cobalt. These tanks must be designed to handle corrosive materials safely.
- Agitation Tanks: To ensure thorough mixing of the ore and chemicals. Proper agitation is crucial for maximizing recovery rates.
Filtration and Drying Equipment
- Filter Presses: Separating solids from liquids after leaching. Filter presses are essential for ensuring the efficiency of the leaching process.
- Dryers: To remove moisture from the extracted cobalt for storage or further processing. Proper drying techniques are essential for maintaining product quality.
Analytical Equipment
- X-ray Fluorescence (XRF) Spectrometer: Analyzing the composition of ore samples and determining cobalt content. XRF is a non-destructive method that provides rapid analysis.
- Atomic Absorption Spectroscopy (AAS): For precise measurement of cobalt concentration in solutions. AAS is widely used for trace analysis and offers high sensitivity.
Conclusion
Understanding magnesite and its beneficiation process is crucial for industries that rely on this valuable mineral. By following the steps outlined in this blog, manufacturers can optimize their processes, improve product quality, and enhance their operational efficiency.
Whether you want to set up a lab for magnesite beneficiation testing or improve your existing processes, having the right knowledge and equipment is essential.
JXSC lab mineral processing equipment manufacturer has more than 38 years of experience in mining processing. We provide various lab mining equipment including gravity-separating equipment for processing minerals such as gold, tin, tungsten, lead, zinc, tantalum, niobium, iron, manganese, silver, titanium-iron, etc. Lab machines include laboratory jaw crusher, hammer crusher, roller crusher, grinding equipment, lab gravity separator, screening, washing equipment, etc. Welcome to consult!