The XFLB Micro Closed-Circuit Continuous Flotation Machine is a state-of-the-art laboratory device for conducting flotation tests on small, representative ore samples. This machine plays a crucial role in mineral processing, allowing researchers and operators to simulate and analyze the flotation process, which is vital for extracting valuable minerals from ores. The results obtained from the XFLB machine can closely represent those from laboratory stand-alone small closed-circuit experiments and semi-industrial experiments, providing valuable data for scaling up processes in industrial applications.
I. Usage XFLB Micro Closed-Circuit Continuous Flotation Machine
This micro continuous flotation machine is particularly beneficial for rapid testing, as it can deliver laboratory or semi-industrial beneficiation indexes in a relatively short period. Its design allows for efficient processing of various materials, including non-ferrous metals, ferrous metals, and non-metallic minerals. The XFLB model is a self-absorbing mechanical stirring continuous flotation machine, meaning it operates efficiently without the need for auxiliary equipment. The flexible configuration of the machine allows users to adjust settings according to specific experimental requirements, making it an ideal choice for both research and industrial applications.
II. Composition
The XFLB micro closed-circuit continuous flotation machine is composed of several key components that work together to ensure efficient operation:
- 1 Set of Slurry Storage Tanks: These tanks are designed to hold the milled slurry before it enters the flotation process. They play a critical role in maintaining a steady supply of slurry for testing.
- 2 Sets of Slurry Mixing Tanks: These tanks are responsible for thoroughly mixing the slurry, ensuring uniformity before it is introduced into the flotation machine. Proper mixing is essential for optimal flotation performance.
- 1 Set of Micro-Medicine Feeders: These feeders deliver precise amounts of reagents and chemicals needed for the flotation process, which can include collectors, frothers, and modifiers.
- 2 Sets of Hose Pumps: These pumps facilitate the continuous transfer of slurry and reagents between the various components of the flotation machine, ensuring a smooth and efficient operation.
- Continuous Flotation Machines: The setup includes a variety of flotation tanks (1-liter with 8 slots, 0.75-liter with 4 slots, and 0.5-liter with 2 slots) that allow for versatile testing and customization based on sample size and type.
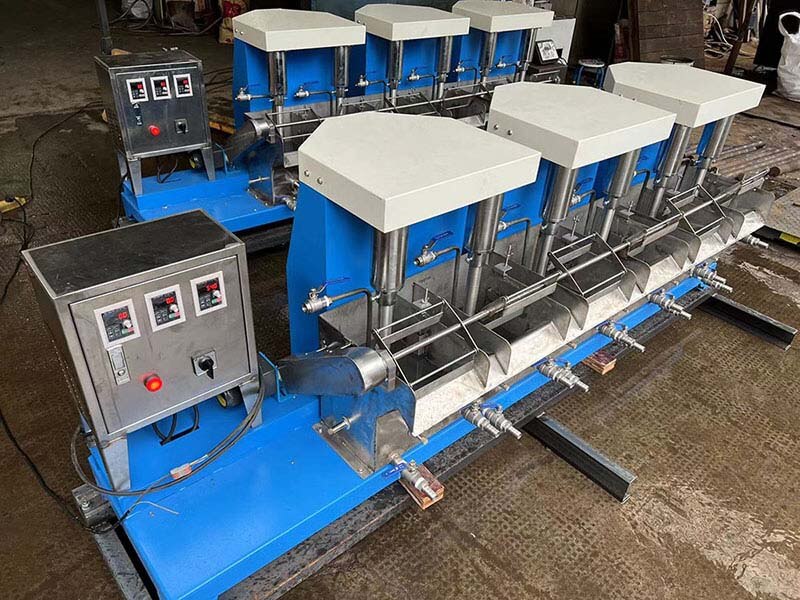
III. Structure
The laboratory XFLB micro closed-circuit continuous flotation machine consists of several integral parts that contribute to its functionality:
- Pulp Storage Tank: This tank stores the milled slurry and is equipped with an impeller to keep the slurry agitated, preventing sedimentation and ensuring consistent feed to the mixing tank.
- Mixing Tank: The mixing tank features a rotating impeller that uniformly stirs the slurry, facilitating the efficient incorporation of reagents and enhancing the overall flotation process.
- Continuous Flotation Machine: This machine operates through a strong self-priming mechanism, created by the negative pressure generated by the impeller’s rotation. This design allows for the effective movement of pulp, foam products, and air suction throughout the system.
- Drug Delivery Machine: This component ensures the precise delivery of flotation reagents, which are crucial for optimizing the separation process.
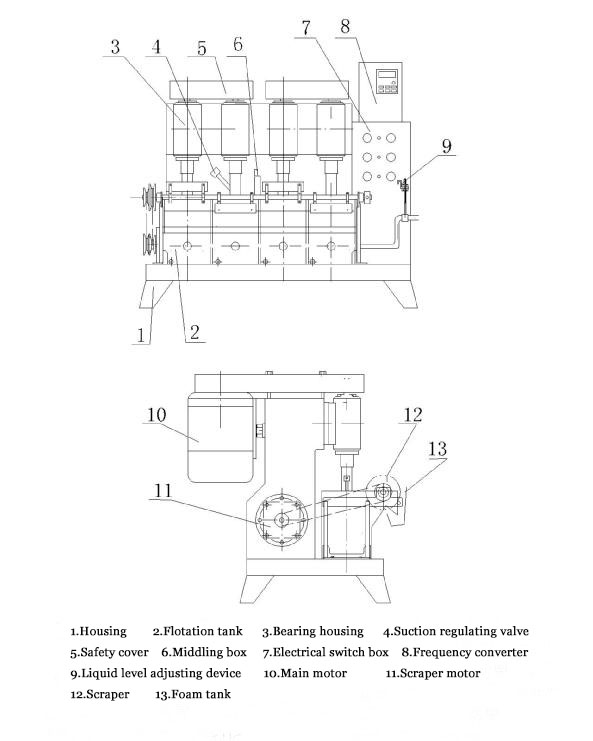
IV. Technical Parameters
The XFLB micro continuous flotation machine has several technical specifications that define its capabilities:
Model | Unit | Flotation Machine Type | Supporting Slurry Storage Tank | Supporting Mixing Tank |
|
| 8 Slots | 4 Slots | 2 Slots |
Volume | L | 1 | 0.75 | 0.5 |
Diameter | mm | 55 | 45 | 45 |
Impeller Speed | r/min | 0-2800 | 1400 | 1400 |
Feed Size | mm | ≤0.3 |
|
|
Power | W | 250 (2 slots) | 750 | 250 |
Capacity | kg/h | 3-5 |
|
|
Weight | kg | 400 |
|
Note: The machine includes a complete set of components, and if a user requires a specific configuration or special combination, they should make a separate request.
V. Operation
The operation of the XFLB micro flotation machine involves several systematic steps:
- Choose Specifications: Based on the pre-programmed process flow, select the appropriate specifications and number of flotation tanks required for the test.
- Arrange Equipment: Set up all flotation machines, pulp storage tanks, mixing tanks, drug feeders, and hose pumps according to the established process flow.
- Set Spindle Speed: Adjust the spindle speed according to flotation requirements. The spindle motor is controlled by a frequency converter, enabling step-less speed adjustments.
- Prepare Auxiliary Equipment: Arrange the water pump, power supply, ore storage, and discharge facilities to facilitate smooth operation.
- Inspect Equipment: Conduct a thorough check of the flotation machine and auxiliary equipment for any damage. Ensure that the rotating spindle operates smoothly, there are no jams, and the liquid levels are properly adjusted without leaks.
- Motor Testing: Check the rotation of the mixing shaft and flotation shaft. Remove the belt cover, switch on the power supply, and adjust the motor pulley to ensure proper rotation. Reattach the belt and cover when confirmed.
- Initiate Flotation Operation: Before starting the experiment, select the flow rate of the dosing machine based on process requirements, set up the necessary pipelines, and pour the slurry into the storage tank. Finally, start the test.
VI. Maintenance and Repair
Regular maintenance and prompt repairs are crucial for the longevity and efficiency of the XFLB micro-flotation machine. Here are key maintenance practices:
- Check Fasteners: Frequently inspect all fasteners to ensure they are tight and secure, preventing unintended malfunctions.
- Inspect Tank and Shaft: Before operation, verify that the tank is free from any obstructions that could jam the shaft. Check that the impeller is properly attached and that there are no air leaks in the inflatable devices or delivery pipes.
- Lubrication: The main shaft bearing should be lubricated with grease every six months. Ensure that the grease melting point exceeds 100°C, and apply an appropriate amount to avoid leakage into the flotation tank. Additionally, add a small amount of dissolving machine oil before each operation of the scraper shaft bearing.
- Clean Equipment: After each experiment, it is essential to clean all components thoroughly. Wipe down and dry all parts to prevent corrosion, contamination, or residue buildup that could affect future tests.
By adhering to these operational and maintenance guidelines, users can maximize the performance and reliability of the XFLB micro continuous flotation machine, ensuring accurate and efficient flotation testing for various mineral processing applications.
JXSC lab mineral processing equipment manufacturer has more than 38 years of experience in mining processing. We provide various lab mining equipment including gravity-separating equipment for processing minerals such as gold, tin, tungsten, lead, zinc, tantalum, niobium, iron, manganese, silver, titanium-iron, etc. Lab machines include laboratory jaw crusher, hammer crusher, roller crusher, grinding equipment, lab gravity separator, screening, washing equipment, etc. Welcome to consult!