what is it
Rotary Vibratory Screen
Max.Feed Size: 20-60 mm
Application: It’s widely used in mining, aggregate production, agriculture, pharmaceuticals, food processing, cement, construction and other industries to separate and classify materials.
Description
Rotary vibratory screen, also known as vibratory Sifter, is a multifunctional device that separates, grades or dehydrates materials according to its physical properties. Its main purpose is effectively and accurately sorting and separating materials into different sizes or grades through vibration. The screen surface of our vibratory screener consists of multiple or multiple layers of wire mesh or perforated panels, available in various sizes and configurations to accommodate different material types and particle sizes. In addition, the vibratory screener has a closed structure with low noise and minimal dust emission, thus creating a more comfortable and safer working environment.
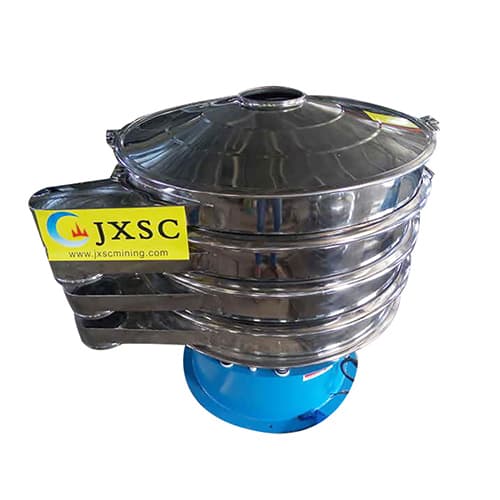
Advantages
Versatility
This rotary vibratory screen can handle fine powders to coarse aggregates; its material form can be bulk solid, powder, liquid or slurry.
Energy saving
Using vibration as the primary method of particle separation is more energy efficient than some other separation technologies.
Ease of maintenance
The screen surfaces can be easily replaced or cleaned and simple maintenance procedures, ensuring that downtime is minimized.
Low cost
Our rotary vibratory screen can save labor costs and improve work efficiency by automating the screening process.
Principle
The rotary vibratory screen works by applying a vibratory force to the screen surface. Put the material into the center of the vibratory screener, and due to the vibration, the particles in the sample start to stratify according to their size. Smaller particles will sink into the screen’s openings and fall, while larger particles will remain on the screen. The particles move and rearrange on the screen surface as the vibration continues. After sieving for a certain period, the machine can be stopped and the collected material analyzed to determine the particle size distribution.
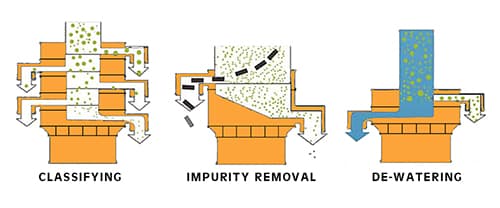
Specification
Model | Diameter (mm) | Effective Aera (m2) | Deck Number | Power (KW) | Max.Feed Size (mm) |
S400-B | 400 | 0.13 | 1-3 | 0.25 | 20 |
S600-B | 600 | 0.16 | 1-3 | 0.5 | 20 |
S800-B | 800 | 0.44 | 1-3 | 0.75 | 30 |
S1000-B | 1000 | 0.63 | 1-3 | 0.8 | 30 |
S1200-B | 1200 | 1.03 | 1-3 | 1.5 | 30 |
S1500-B | 1500 | 1.65 | 1-3 | 2.2 | 50 |
S1800-B | 1800 | 2.4 | 1-3 | 2.5 | 50 |
S2000-B | 2000 | 2.98 | 1-3 | 2.5 | 60 |